Laserbasierte Silizium-Kristallisation für die monolithische Integration bei MEMS-Sensoren
Im Gegensatz zu sonst üblichen Verfahren entfallen Drähte und Lötstellen – was die Bauteile perspektivisch kleiner und leistungsfähiger macht.
Zur Messung von Bewegungen sind MEMS-Inertialsensoren zu Milliarden in Fahrzeugen und Consumer-Produkten eingebaut. Damit die MEMS-Sensoreinheiten diese Aufgaben zuverlässig und prozesssicher bewältigen können, werden sie mit einem elektronischen, anwendungsspezifischen, integrierten Schaltkreis, kurz ASIC, kombiniert, der auf einer Silizium-Trägereinheit, dem Wafer, sitzt. Weil die Umgebungstemperatur in der Nähe des integrierten Schaltkreises mit seinen temperaturempfindlichen CMOS-Transistoren jedoch 450 Grad Celsius nicht überschreiten darf, werden MEMS-Sensoren aus kristallinem Silizium aufgrund der konventionell hohen Herstellungstemperaturen zunächst separat hergestellt. Anschließend folgt das Kontaktieren mit dem Schaltkreis via Draht- und Lötverbindungen oder Waferbondverfahren.
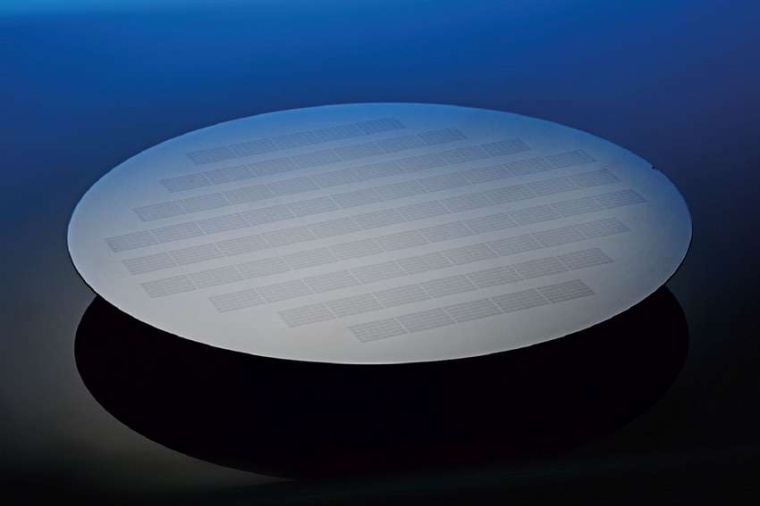
„Die konventionelle Verbindungstechnik benötigt jedoch viel Platz und verhindert eine weitere Miniaturisierung der MEMS“, erklärt Florian Fuchs vom Fraunhofer-Institut für Lasertechnik. MEMS aus kristallinem Silizium lassen sich daher bisher nicht direkt auf dem ASIC aufbauen. Wegen der Temperaturinkompatibilitäten im Herstellungsprozess sind somit der weiteren Miniaturisierung und Leistungssteigerung der Sensoren Grenzen gesetzt.
Als Alternative zu konventionellen Fügetechniken setzt das Fraunhofer-ILT auf ein laserbasiertes Verfahren, das es ermöglicht, MEMS-Sensoren aus kristallinem Silizium direkt – also monolithisch – auf den temperaturempfindlichen Schaltkreisen aufzubauen. Dabei liegen die Projektschwerpunkte in der Abscheidung von Si-Schichten durch das Fraunhofer-Institut für Schicht- und Oberflächentechnik und Fraunhofer-Institut für Siliziumtechnologie, der selektiven Laserkristallisation durch das Fraunhofer-ILT und der Auslegung sowie der mikroelektronischen Weiterverarbeitung der Schichten zu Sensoren durch das Fraunhofer-ISIT.
Die Forscher machen sich dabei die Tatsache zunutze, dass sich amorphe Siliziumschichten bereits bei niedrigen Temperaturen unterhalb von 450 Grad Celsius auf dem schaltkreistragenden Wafer bei hohen Abscheideraten herstellen lassen. Der Laser kristallisiert nicht nur diese Siliziumschicht, sondern aktiviert auch die darin enthaltenen Dotierstoffe und sorgt damit für eine geeignete elektrische Leitfähigkeit. Anschließend folgt das Freistellen der Sensoreinheiten mit Hilfe klassischer mikroelektronischer Fertigungsverfahren.
Die Hochtemperatur-Kristallisation mittels Laserstrahlung unterhalb des Schmelzpunktes von Silizium geschieht ortsselektiv und sehr schnell – im unteren Millisekundenbereich –, sodass sie im Zusammenspiel mit gezieltem Temperaturmanagement die empfindliche Elektronik auf dem darunter liegenden Substrat nicht beschädigt und mechanische Spannungen im Schichtmaterial minimiert. Die Kristallisation läuft mit einem fokussierten Laserstrahl mit einem Durchmesser von einigen zehn Mikrometern ab, der spiegelgelenkt die gesamte Oberfläche schrittweise abfährt. Die Wärmeabfuhr geschieht bei diesem ortsselektiven Prozess effektiv in drei Raumrichtungen. Das unterscheidet das Verfahren von alternativen photonischen Verfahren wie der Blitzbelichtung, bei der die Wärmeabfuhr aufgrund der großflächigen Bearbeitung nur in eine Richtung stattfinden kann.
„Aufgrund der sehr schnellen Energieeinbringung in nur ein kleines Volumenelement erzielen wir mit der Laserbearbeitung eine Festphasenkristallisation des Siliziums bei Temperaturen, die oberhalb der Zerstörschwelle des darunterliegenden Schaltkreises liegen. Aufgrund der kurzen örtlichen Bearbeitungszeit wird dieser dennoch nicht geschädigt“, erklärt Christian Vedder vom Fraunhofer-ILT. Das neu entwickelte Laserverfahren verringert die elektrischen Widerstände der Silizium-Schichten um mehr als vier Größenordnungen. Aus diesen Schichten konnten MEMS-Sensoren mit typischen Fingerstrukturen für einen kapazitiv arbeitenden Beschleunigungssensor hergestellt werden.
„Die Fähigkeit, kristalline Siliziumschichten unter CMOS-kompatiblen Bedingungen auf einem ASIC-Wafer herzustellen, eröffnet neue Möglichkeiten für die MEMS-IC-Integration, da Eingriffe in die CMOS-Herstellungsprozesse entfallen“, sagt Fuchs. Die dadurch wegfallenden Prozessverschränkungen erlauben eine unabhängige Entwicklung von MEMS und IC und stellen damit eine deutliche Reduzierung der Entwicklungszeiten und -kosten in Aussicht. Neben einer höheren Integrationsdichte lässt die Einsparung von Drahtverbindungen und Bondpads zudem geringere parasitäre Störgrößen sowie eine verbesserte Abschirmung gegen elektromagnetische Störfelder erwarten, was sich positiv auf die Signalqualität und das Driftverhalten der Sensoren auswirkt.
Die gewonnenen Erkenntnisse lassen sich künftig in mehrere Richtungen vertiefen und weiterführen. Interessant wäre beispielsweise die Anpassung des Verfahrens an die spezifischen Anforderungen unterschiedlicher Sensortypen mit anderer Schichtdicke oder anderen Dotierstoffen. „Wir suchen nun Anwender aus der Industrie, mit denen wir das im Team entwickelte Verfahren gewinnbringend für ihre Produkte einsetzen können“, so Fuchs.
Der Ausblick auf Leistungssteigerung bei gleichzeitiger Miniaturisierung macht die MEMS-Technologie auch für weitere Einsatzfelder interessant, deren Anforderungen heutige MEMS-Systeme noch nicht erfüllen können. Denkbar wäre der Einsatz im Bereich des autonomen Fahrens, bei dem sehr genau arbeitende Beschleunigungssensoren die Empfangslücken des GPS-Signals in Tunneln oder Parkhäusern überbrücken könnten. Interessantes Potenzial bietet das Verfahren auch in der Medizintechnik, um etwa Temperatursensoren in Kopfhörer zu integrieren und die gewonnenen Daten zur Überwachung von Patienten oder zur Pandemiebekämpfung zu nutzen. Außerdem könnten miniaturisierte, hochpräzise Beschleunigungs-MEMS-Sensoren die genaue Lokalisation von Einsatzkräften der Feuerwehr in brennenden Gebäuden ermöglichen und damit die Sicherheit von Einsatzkräften erhöhen.
Fh.-ILS / RK
Weitere Infos